Innovation or Renovation?
Jeffery A. Hite, Director of Technical Promotions, Rinker Materials
Trygve Hoff, P.E., Northeast Region engineer, ACPA
Douglas Holdener, P.E., Florida Engineer, ACPA
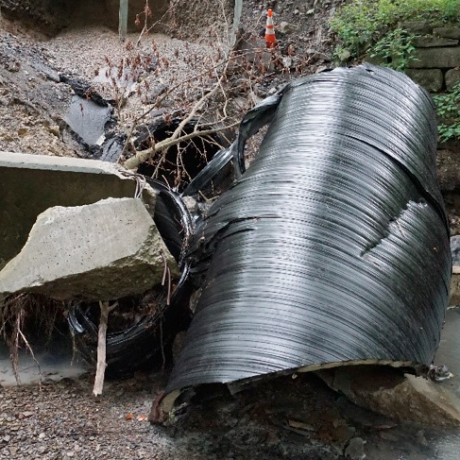
Washed out and destroyed 48-inch diameter HDPE pipe with a “honeycomb wall” design (AASHTO M294 Type D).
Early and notable concrete pipe projects included Henry Flagler’s Florida East Coast (FEC) Railroad, the Southern California Edison power facility in San Onofre, and the Gwynns Falls Interceptors in Baltimore. Civil engineering advancements led to notable concrete pipe milestones such as increased diameters, higher strength classes, internationally recognized design standards, deeper installation designs, radius/skew pipe, zero cover traffic applications, and microtunnel/jacking installations. At times, special project circumstances have driven the need for special designs and manufacturing. However, the fundamental principles of concrete pipe design, installation, and performance have proven to be so resilient and reliable that there has been no need to reinvent or overhaul. Concrete pipe is inherently strong, and resilient, and has been the benchmark of performance.
In stark contrast, over an approximate 20-year span, there has been a revolving pattern of unveiling, re-tooling, and repeating different versions of corrugated plastic storm pipe products. For example, a combined 18 different corrugated plastic pipe products have been introduced by two major plastic pipe manufacturers with most of those products seeming to have “come and gone.” According to the plastic pipe industry, and the ASTM standards that they develop, its products should structurally function, assuming they are installed correctly, at great depths, under significant live loads, and remain durable for 100 years, possibly even 2,893 years (ACPA YSK 142)[1]. So why have there been numerous structural failures of different plastic pipe versions, and why do they slightly differ – yet still flexible – plastic pipes get introduced only to cannibalize the older product versions? Here are three examples of different plastic pipe designs that have experienced significant structural failures.
As the first example, a 48-inch diameter HDPE pipe with a “honeycomb wall” design (AASHTO M294 Type D) washed out at a culvert crossing SR 3054 (Baldwin Road)in Collier Township, Pennsylvania following an intense rainfall event in June 2018. The HDPE culvert was installed in 2008 to add flow capacity to the existing 54-inch diameter concrete pipe culvert. Despite the HDPE culvert installation achieving only a short 10-year service life, the existing, adjacent concrete pipe culvert survived the extreme rainfall event (likely, due to its inherent mass) and remains structurally viable and fully functional. When the HDPE honeycomb wall pipe was introduced to the marketplace, it was purported that “the strength of its design structure is invisible in the manufactured product.”.
Failed dual run of 54-inch HDPE storm sewer pipe with rib stiffeners in the CrownPointe Commerce Park in Orlando.
As a second illustration of a concerning pattern, in early 2018, it was confirmed that a dual run of 54-inch HDPE storm sewer pipe failed, and even collapsed in some sections, in the CrownPointe Commerce Park in Orlando, Florida. Over 1,600 feet of HDPE pipe was replaced with concrete pipe in June 2018 at the property owner’s expense. This particular HDPE pipe appears to be a variant version of a standard pipe in that its outer corrugation crests were augmented with “corrugation stiffeners” resembling smaller inverted corrugations. The installation was in an industrial facility with tractor-trailer traffic and installed with 2.5 to 4-feet of cover. The pipe was installed in 1998, and product literature in 2005 claimed that 54-inch HDPE pipe was “rated” for highway traffic loads at only 18 inches of cover. The pipe was heralded as providing “superior value while providing physical strength, structural design and up to a 100-year service life that just cannot be matched by metal or concrete.”
Fort Myers completed the $5.4M installation of 11,672 feet of concrete pipe to replace a failing HDPE storm sewer.
And, as an example of a third version of corrugated plastic pipe involved in a significant failure, in early 2018, the City of Fort Myers, Florida completed the $5.4M installation of 11,672 feet of concrete pipe to replace failing HDPE storm sewer (AASHTO M294 Type S) on McGregor Boulevard. Over an approximate 20-year span since the initial HDPE pipe installation, the City made many emergency repairs to failed sections of the HDPE storm sewer. The decision to replace the entire 2.2-mile stretch was made after super tidal events exacerbated the compromised storm sewer sections. Product claims for this version of HDPE pipe purported that it was “suitable for use under both H20 and E80 live loads, or with fill heights in excess of 50 feet.”
Each version of corrugated plastic pipe has been heralded with claims such as “superior” to concrete, “high capacity,” lightweight advantage, and durable under loads ranging from shallow to deep fills for 100 years. With each new version, there are still new structural concerns. Why would recent resin modifications, such as post-consumer recycled resins and polypropylene resins, make these products more durable? Perhaps the real problem is that the engineering community has never been fully informed by the plastic pipe industry about the proper design and specification of plastic pipe installations, and in some cases, even allowed to believe that plastic pipe and concrete pipe can be installed similarly. When referring to installation guidelines, one will find that this is not the case.
You be the judge. Some may claim that concrete pipe is old. We agree, concrete pipe continues to improve on a proven product.
Photos: Courtesy of the ACPA and its members
[1] ACPA, You Should Know Bulletin 142, HDPE Pipe Service Life, Facts and Conclusions, 2007